Exploring Temperature-Controlled Concrete and Its Versatile Applications
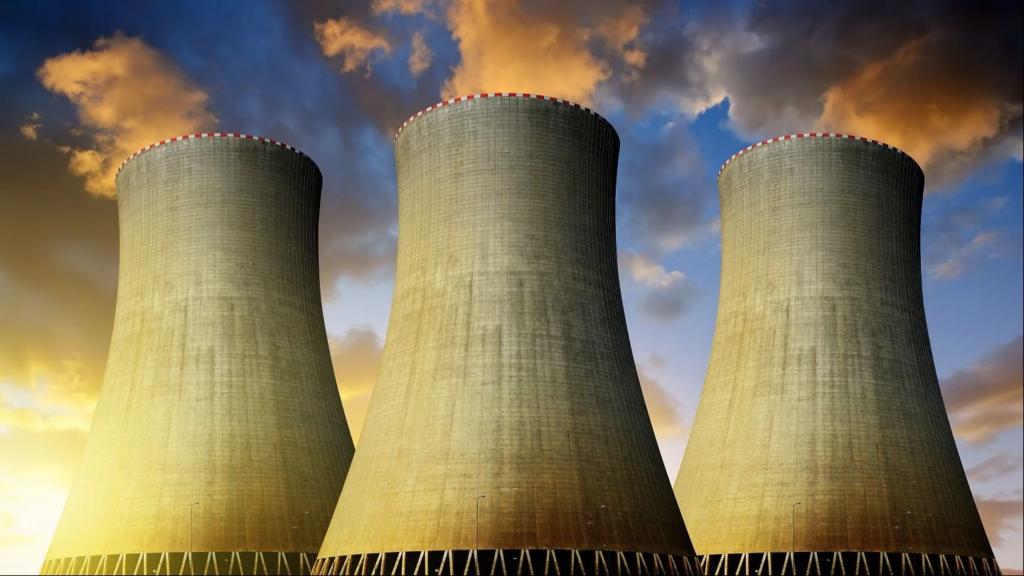
April 12, 2024
Traditional concrete, when exposed to high temperatures, experiences rapid hydration, leading to a phenomenon known as the “heat of hydration.” This process generates excessive internal heat within the concrete, causing various problems such as thermal cracking, and delayed ettringite formation (DEF).
Here’s where Temperature-Controlled Concrete (Temperature Controlled Concrete) emerges as a game-changer. As the name suggests, Temperature Controlled Concrete is a specially formulated concrete designed to mitigate the negative effects of high temperatures during the curing process.
How Does Temperature-Controlled Concrete Work?
Temperature Controlled Concrete employs a multi-pronged approach to manage heat of hydration and ensure optimal concrete performance in hot weather conditions:
Low Heat Cement: The formulation utilizes specially selected cements with a lower heat of hydration compared to standard Portland cement. This reduces the peak temperature reached during the setting process.
Supplementary Cementitious Materials (SCMs): Temperature Controlled Concrete incorporates SCMs like fly ash or slag. These materials not only contribute to lower heat generation but also enhance the overall strength and durability of the concrete.
Chemical Admixtures: Specific admixtures are included in the mix to control the setting time and rate of hydration. These admixtures allow for better control over the heat generation process.
Ice Flakes or Chilled Mixing Water: In extreme cases, incorporating ice flakes or chilled mixing water can further reduce the initial temperature of the concrete mix.
Benefits of Using Aparna RMC’s Temperature-Controlled Concrete:
Minimized Thermal Cracking: By regulating the heat of hydration, Temperature Controlled Concrete significantly reduces the risk of thermal cracking, leading to a more robust and durable concrete structure.
Enhanced Workability: The specialized blend ensures optimal workability even in high temperatures, allowing for efficient pouring and finishing of the concrete. This translates to faster construction times and reduced labor costs.
Improved Durability: Temperature-controlled concrete promotes long-lasting concrete structures by minimizing internal cracks and enhancing resistance to water and chloride ingress. This translates to lower maintenance requirements over the lifespan of the building.
Superior Strength Properties: Temperature Controlled Concrete offers various strength advantages:
Higher Flexural Strength: Provides superior resistance to bending and deformation.
High Impact Resistance: Can withstand strong forces without compromising structural integrity.
High Tensile Strength: Offers exceptional resistance to pulling forces.
Enhanced Work Efficiency: Consistent workability due to temperature control allows for faster construction timelines, leading to improved project completion rates.
Resistance to Abrasion and Impact Loads: Ideal for high-traffic areas like floors and pavements, and structures exposed to wear and tear.
Versatile Applications of Temperature-Controlled Concrete
While Temperature Controlled Concrete excels in mitigating the challenges of hot weather construction, its benefits extend far beyond the scorching summer months. Here’s a closer look at how Temperature Controlled Concrete proves to be a valuable asset in various applications:
Hospital Constructions: Hospitals require specialized construction techniques to prioritize patient safety and optimal functionality. Building radiation walls presents a unique challenge, demanding precise concrete temperature and workability. Temperature Controlled Concrete rises to this challenge by allowing for meticulous control of the concrete’s internal temperature during the curing process. This precise temperature regulation is essential for ensuring the effectiveness of the radiation-shielding properties of the wall. Additionally, Temperature Controlled Concrete’s ability to minimize cracking risk safeguards the structural integrity of the wall, preventing potential leaks or compromises in radiation shielding.
Nuclear and Thermal Power Plant Constructions: In nuclear and thermal power plants, concrete faces a unique challenge: maintaining structural integrity under both operational and potential accident scenarios. To address this, temperature controlled concrete is employed. This specialized mix incorporates techniques like special ingredients and curing methods to manage heat generation during setting and ensure the concrete can withstand the moderate temperatures of normal operation.
Mass Concreting Applications (Raft Foundations): For massive concrete pours like raft foundations, traditional concrete suffers from internal heat buildup, leading to potentially disastrous thermal cracks. Temperature Controlled Concrete combats this by regulating heat of hydration, significantly reducing the risk of cracking. This translates to a more robust and stable base for the entire structure, ensuring long-term durability and minimizing future maintenance costs. Additionally, Temperature Controlled Concrete maintains optimal workability even in large volumes, allowing for efficient pouring and finishing, saving valuable time on the construction schedule.
High-Rise Buildings: As high-rise buildings climb skyward, the sheer weight of concrete itself contributes to internal heat generation in lower sections. This unseen enemy can jeopardize structural stability if left unchecked. Temperature Controlled Concrete tackles this challenge head-on by regulating heat of hydration. This meticulous temperature control minimizes thermal cracking risks in crucial load-bearing elements, safeguarding the structural integrity of the entire building. Furthermore, controlled heat distribution throughout the concrete pour prevents uneven thermal expansion and contraction, ensuring overall structural stability. In some formulations, Temperature Controlled Concrete can even offer enhanced fire resistance, a vital consideration for high-rise structures where fire safety is paramount.
Infrastructure Projects: Bridges, dams, and other critical infrastructure projects rely heavily on massive concrete structures that are constantly exposed to harsh environmental conditions. Here, even minor cracks can have disastrous consequences. Temperature Controlled Concrete emerges as the ideal choice for such applications due to its superior durability in demanding environments. By minimizing internal cracks, Temperature Controlled Concrete reduces the need for frequent repairs and maintenance, leading to significant cost savings over the project’s lifespan. This exceptional performance contributes to the overall longevity and reliability of bridges, dams, and other vital infrastructure projects, ensuring they serve their communities for generations to come.
In conclusion, Temperature Controlled Concrete transcends the limitations of seasonal challenges, offering a versatile solution for diverse construction projects. Its ability to manage heat of hydration, enhance workability, and promote long-term durability makes it a valuable asset for building strong, dependable structures across various applications.
Choose TempCrete by Aparna RMC
Aparna RMC‘s TempCrete goes beyond a typical temperature-controlled concrete solution. Their meticulous formula, combining low-heat cement, SCMs, optimized admixtures, and temperature control measures, ensures exceptional performance. TempCrete minimizes thermal cracking, maintains workability in hot weather, and offers superior strength properties.