How Quality Control Ensures Strength and Consistency in RMC
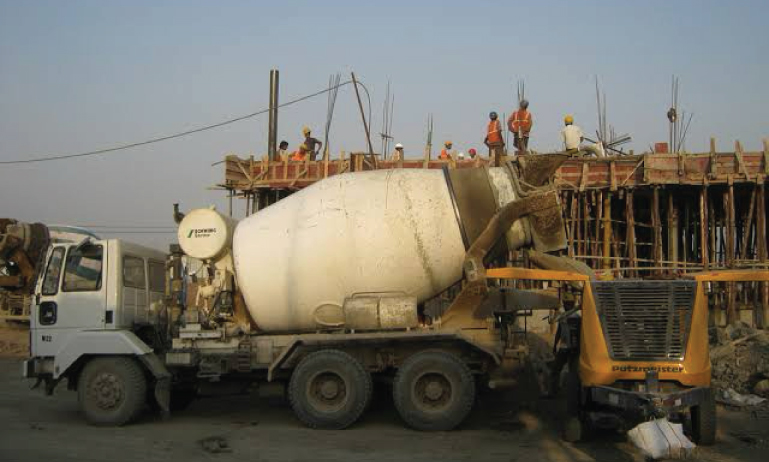
February 1, 2024
When construction demands predictable strength, reliability, and on-time project completion, ready-mixed concrete (RMC) becomes the material of choice. But these benefits don’t happen by chance – rigorous quality control at every phase of production separates premium RMC from the inconsistent results produced by on-site mixed batches.
Conventional mixed concrete, even when done with care, cannot compete with the level of accuracy and control achieved in a modern RMC batching plant. Variations in raw material sources, batch proportions, and even basic mixing techniques make site-mixed concrete a risk in projects where uniform strength, workability, and durability are non-negotiable.
In contrast, high-grade RMC suppliers approach their materials, design, and production with almost scientific precision. Their facilities prioritize testing, technology, and a multi-level approach to quality assurance. These collective efforts contribute to a final product that delivers consistent and guaranteed concrete for your project requirements.
How RMC Quality is Tested
A dedicated plant team works to manage quality, with dedicated QA/QC staff overseen by the Quality Assurance/Quality Control Manager. Quality control of ready-mixed concrete may be divided into three phases. Each phase of production plays an integral part:
1. Forward Control:
Forward control and consequent corrective action are essential aspects of quality control. Forward control includes the following.
Ingredient Test: Suppliers don’t skip incoming material verification. Whether it’s the cement arriving from a trusted source, aggregates of various sizes, sand, supplementary cementitious materials, or carefully measured admixtures, all are tested against industry standards before reaching the plant’s systems.
Raw Material Inspection: Bulk cement storage silos prevent moisture damage, while dedicated stockpiles segregate aggregates of different grades. Even water purity is actively managed to avoid introducing contaminants into the mix.
Calculated Design: Mix design software allows engineers to fine-tune proportions based on the target strength (e.g. M25, M40 grade concrete) and other performance needs. They factor in desired workability, exposure conditions, and even local material characteristics.
Precision Equipment: Automated batching plants meticulously weigh and dose ingredients according to the computer-designed measures, avoiding human error that might happen during manual operations.
2. Immediate Control
Immediate control in concrete quality control refers to taking immediate action to control the quality of concrete that is being produced or delivered right after.
Production Control:
Process Parameter Scrutiny: Technicians diligently track batch size, water-cement ratio, mixing time, and other processing variables. Every step must align with the specifications of the mix design to ensure concrete meets its engineered target strength and workability.
Batch Inspection: Before a truck pulls away, visual inspection is mandatory. Experienced eyes assess the concrete’s uniformity, cohesion, and overall consistency. This preliminary check can expose segregation, insufficient mixing, or workability issues.
Product Control:
RMC plants don’t rely solely on observation. These tests provide critical quantitative data:
Slump Test: This widely used test determines the flowability and ease of placement of concrete. Different cone shapes are common (e.g., standard slump cone, K-Slump Tester) depending on the concrete type. Target slump values for various applications are defined in standards and adjusted during the production phase if needed.
Density, Temperature, and Air Content: For specialized RMC, fresh concrete density (how much it weighs per unit volume) is often tested. Temperature significantly impacts setting time and must be closely controlled, even using iced water or chilled aggregates in hot weather. In freeze-thaw environments, air entrainment testing verifies that microscopic air bubbles have been correctly introduced to the mixture, enhancing durability.
3. Retrospective Control:
Retrospective control is concerned with those factors that influence the control of production. This might involve various procedures:
Quality Sample Testing: One of the most important retrospective tests is crushing cubes or cylinders of hardened concrete after 28 days. This isn’t possible to do until days or weeks after the concrete is placed, but it indicates if it actually achieved the strength grade it was designed for.
Strength Check-ups: Testing might also revisit initial properties like the slump test results, air content, or aggregate properties from previous batches. Analyzing why they differed and how they influenced strength provides valuable insights.
Materials Checks: Retrospective control extends beyond the concrete itself. Regular ‘weighbridge’ audits compare incoming raw material (cement, aggregates) at the plant versus the quantity of concrete that was transported out by trucks. Stockpiles are periodically measured to spot discrepancies.
Diagnosis and Correction: This isn’t just collecting data for the sake of it. The goal is identifying patterns. Are strength results drifting lower over time? Maybe specific equipment needs recalibration or material sources are inconsistent. These findings prompt proactive changes to avoid errors before they cause larger problems.
Choose Quality; Choose Aparna RMC
The next time your project needs concrete, don’t simply focus on the price. Look for RMC suppliers that prioritize quality control from materials to pouring. Their focus will contribute to your project’s long-term success and structural integrity for years to come. Aparna RMC is known for superior service enabled by digital tools, along with an ISO Certified process that guarantees consistent quality and timely delivery across its 29 plants spread across four states.